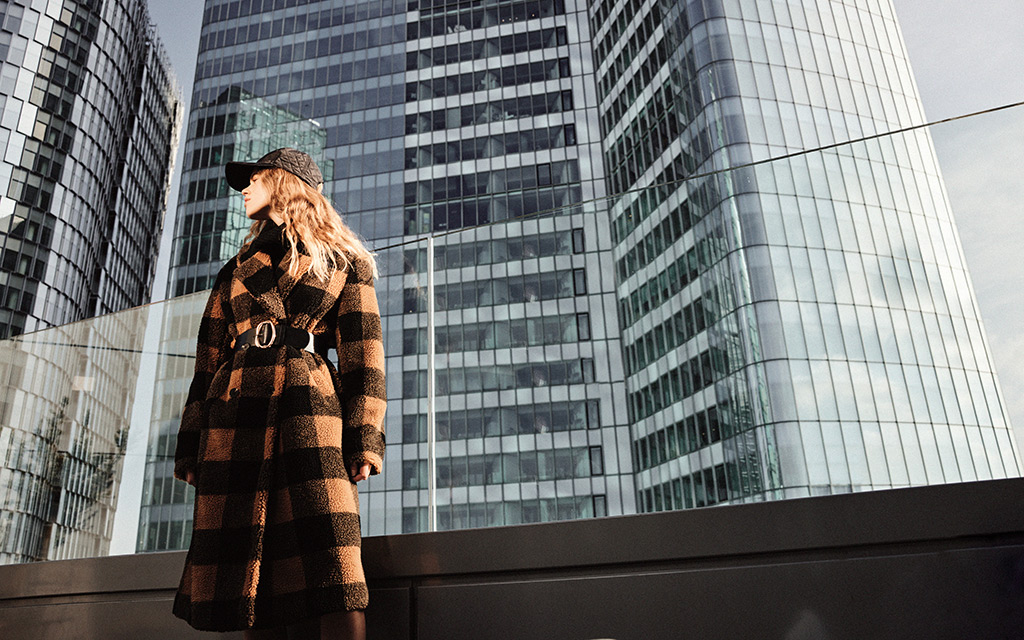
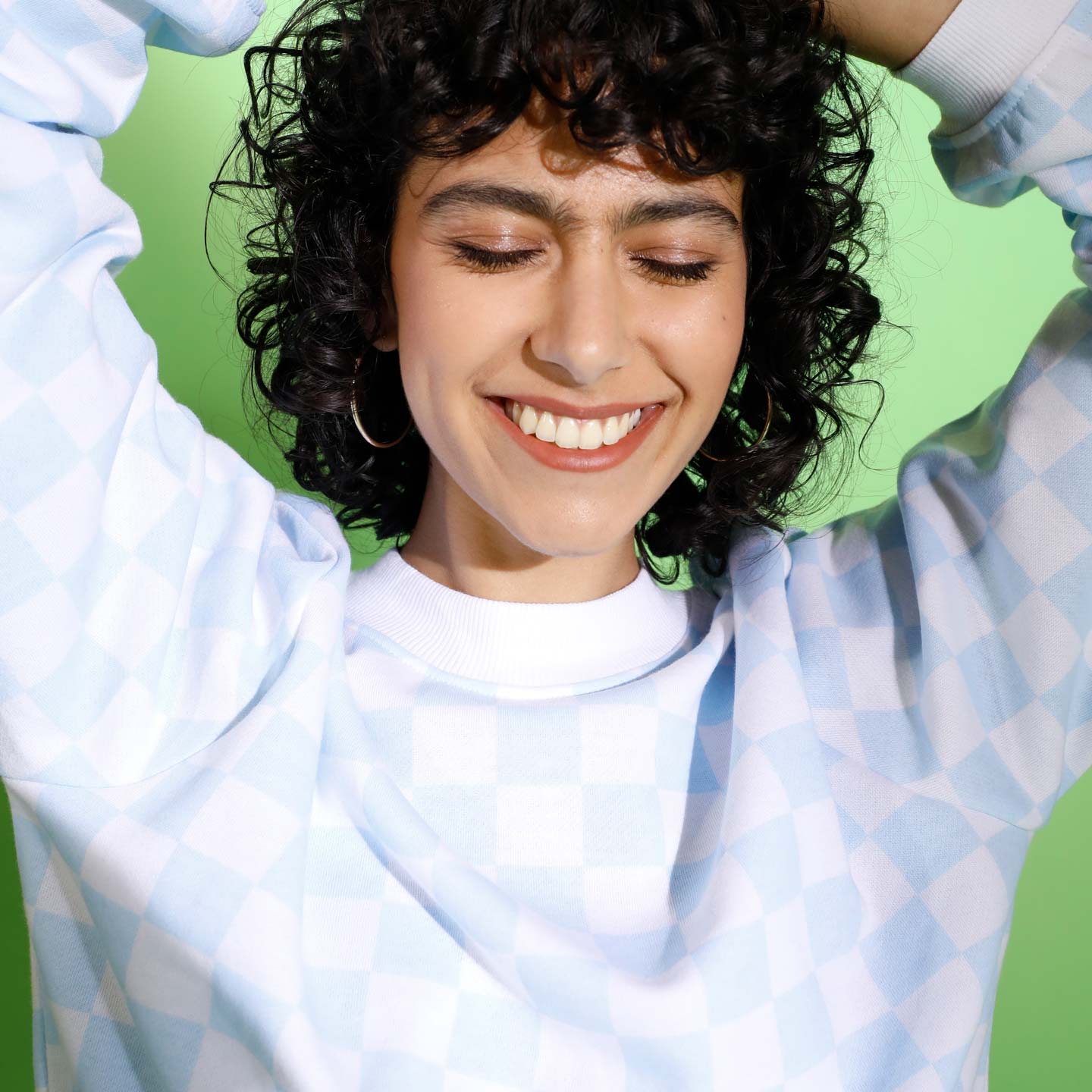
Various studies and analyzes by textile engineers have enabled us to select the fibers below, our goal being to choose the options that allow us to combine the reduction of environmental impact, the quality of the fibers, and the optimization of our purchase costs.
In 2020, we used for the first time recycled fibers to make garments, and our first ambition was to have at least 10% of recycled fibers in our collections: goal achieved (13%) ! In 2021, we wanted to go further, trying to reach 25% of recycled fibers in collections: goal achieved again (27%)! In 2022, we want to integrate at least 30% of recycled fibers, to progressively reach 100% in 2030.

Since 2020, our collections have been containing EcoVero®-certified viscose. For your info, viscose is an artificial fiber which combines both synthetic and natural components, such as wood. The EcoVero® label certifies that the wood used comes from sustainably managed forests that are FSC (Forest Stewardship Council) or PEFC (Pan European Forest Certification) certified. More information is available on the Ecovero.com website if you’d like to find out more!
In 2021, we wanted that 100% of viscose used in our collections has a reduced environmental impact: as for today, we integrated 12% of EcoVero viscose.
Some of our jeans benefit from a “Better wash” process: this is the name we give at Pimkie’s to a denim washing process which reduces the water consumption compared to an usual washing… but not only ! This is a more responsible treatment, compared to conventional ones used at jeans finishing stage:
- - as we said, reduction of water consumption
- - reduction of energy consumption
- - reduced impact on workers health
To go further, we use EIM (Environmental Impact Measuring software) developed by Jeanologia, a textile innovative company (especially on denim).
This software has specially been conceived for textile embellishment factories, in order to help them set up more sustainable process (more info on https://www.jeanologia.com/eim).
n 2020, we became members of BC (Better Cotton), an initiative to promote cotton that is less environmentally-damaging and more profitable for farmers than standard cotton which is widely used in the textile industry. This is just a temporary solution until we find ways to do even better and to keep on reducing our impact, again and again.
Farmers are Better Cotton-certified, not the cotton, that means these farmers are trained and authorized to use Better Cotton production processes, but they can also use other processes. The brands therefore commit to source cotton from BC-certified producers.
In 2021, we were committed to source 30% of the cotton used in our collection from BC supply chain: we finally reached 39%! For 2022, we want to stabilize this commitment level.
Bear in mind that Better Cotton is a gradual solution: we’re making progress step by step, slowly but surely, and our ultimate goal is to use only recycled cotton.
As you know, at Pimkie, we really care about the quality of the products made. At least 80% of ordered products are checked on the production line before shipping. We also regularly check products as they arrive, especially those that are complicated to manufacture, to make sure you receive the perfect product!
Pimkie products comply with the European REACH regulation which aims to limit the use of harmful chemicals in products. But we didn’t stop there, we’ve also included other chemicals using the Oekotex label in our specifications, which you can read here if you’d like.
What is sandblasting? It’s the process of softening and lightening the colour of a fabric. In the textile industry, it is used to wear out, wash or bleach denim by propelling a high-pressure stream of abrasive material, namely sand, at the garment. The problem is that this widely-used method is harmful because the workers exposed to it, often without protection, inhale toxic dust, which causes serious or even fatal diseases. This technique is now banned from our factories to protect our worker's health.
It's true that it’s difficult to have total control over our entire production chain. But we still ask our suppliers not to use cotton from Uzbekistan, Syria or Turkmenistan, basically, areas that could be problematic from a social and environmental perspective. Depletion of the Aral Sea, forced labour, child labour, funding terrorism, etc. We also make sure not to work with suppliers or factories in North Korea, and, of course, we have banned all raw materials from the Xinjiang province in China, as well as all subcontracting and production in this region, due to forced labour activities detected by NGOs.
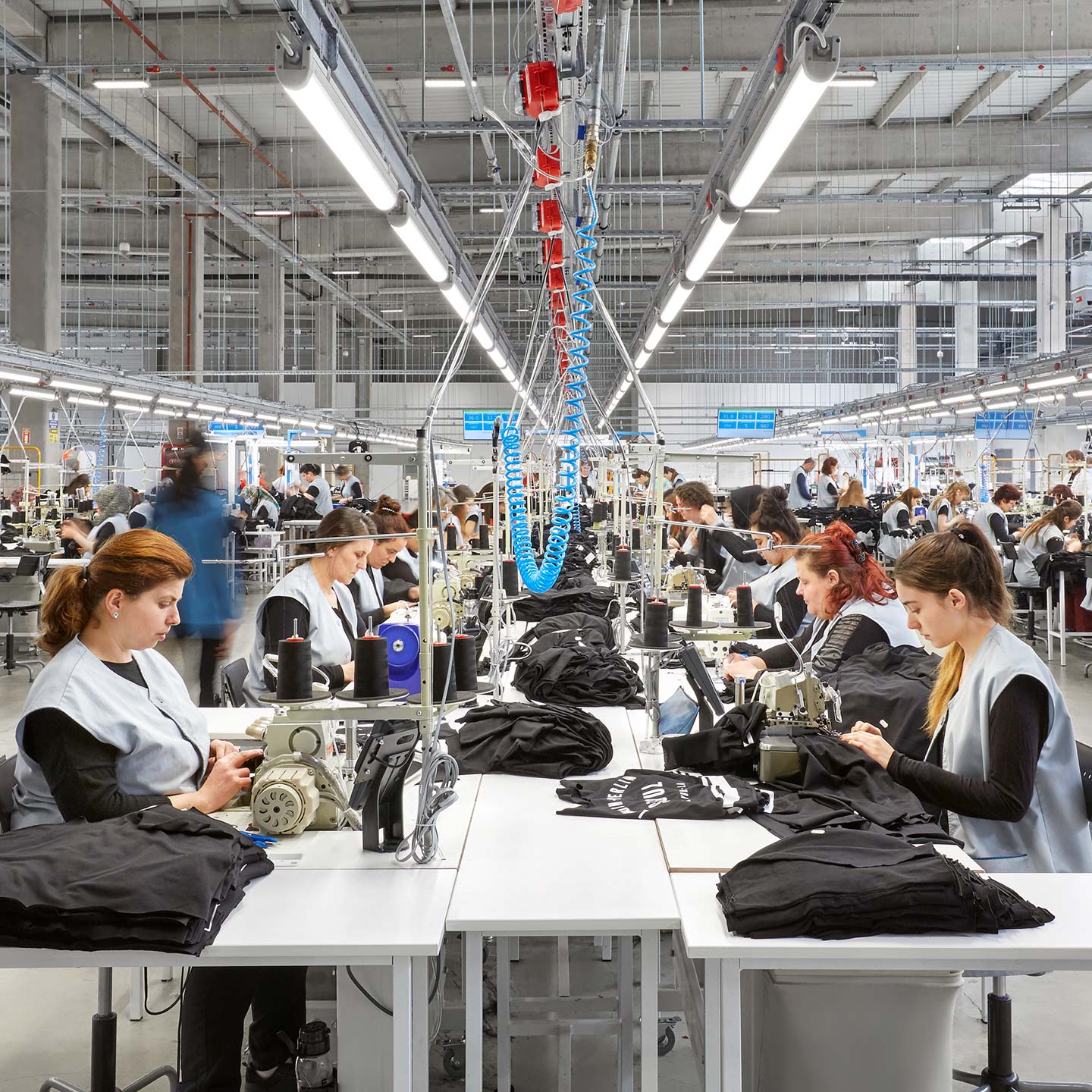
You probably don’t know this, but our external suppliers and factories cannot start an operation for Pimkie without prior approval from our CSR team - Corporate Social Responsibility. For this purpose, a social audit is carried out in accordance with the ICS standard, which includes around forty brands (more info at www.ics-asso.org)). The audit is based on our supplier code of conduct, taken from the guiding principles of the OECD, the Universal Declaration of Human Rights and the ILO regulations, (International Labour Organisation), as well as national laws when they offer better conditions for employees.
During these audits, many issues are reviewed, such as child labour, workers’ health and safety conditions, pay and working hours, freedom of association, forced labour, discrimination and disciplinary practices. Our supplier code of conduct is available here. In short, the document includes the supplier code of conduct, our policy on forced labour, child labour and young workers, and guidelines on the environment and the use of chemicals.
We carry out these audits throughout our relationship with a factory to regularly check that everything is OK. For example, for new factories, the audit is done before operations begin and we only start working together if a score of A, B or C is obtained. For A & B factories, a new audit is carried out every 2 years. For C factories, a new audit is carried out within 1 year, and within 3 months for D factories. For E factories, immediate proof of resolution of the critical deviation is required and an audit must be carried out within 1 to 3 months depending on the nature of the deviation so that we can continue working with them.
All audits are carried out on a “semi-announced” basis, i.e. the factories are notified of the audit but are not given a specific date. They only know that it will take place within a 3-week window. In the event of non-compliance with our requirements, a Corrective Action Plan is initiated. If the plan is not implemented within the agreed timeframe, we cease all business activity with the factory in question until it is brought back into compliance. Want to find out more? Check out the list of factories and social audit results.It is updated every 6 months and it lists 100% of the known factories we work with right now. However, as we like to be sure, we still carry out regular visits during production and, if an anomaly is found, the suppliers concerned are subject to a specific support plan. In the event of a repeated or serious breach of regulations (child labour, forced labour, etc.), non-compliance with the code of conduct, or non-compliance with their contractual obligations, French law authorises us to terminate any commercial relationship with the supplier or factory concerned. In this case, a period of notice is given according to the length of the business relationship and the turnover achieved in the last 3 years. Nonetheless, throughout the period of notice, a commitment is made to maintain a certain level of turnover.
To give you an idea:
- in 2018 and 2019: 100% of the factories audited, compliance rate of 90%
- in 2020, 100% of the factories, compliance rate of 97%
-in 2021, 100% audited factories, compliance rate of 99%
We are making gradual progress in identifying our production chain: we should soon be able to publish a list of Tier 2 factories which we work with, i.e. factories that dye fabrics, that supply threads, etc., to garment factories.
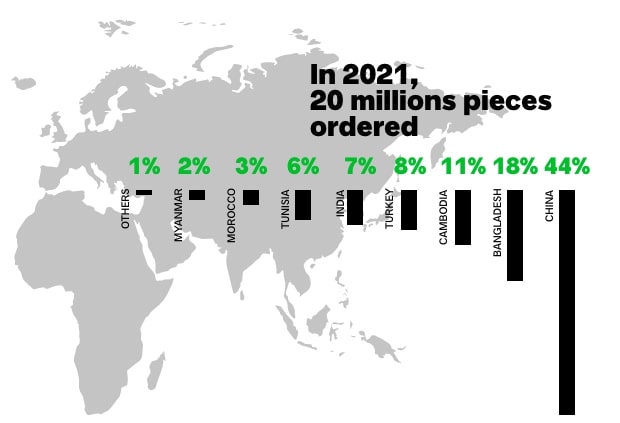
To encourage companies to make progress, we’ve set up a special funding scheme for our suppliers. It is based on the principles of “reverse factoring”, i.e. suppliers have the option to pay their invoices early at a preferential price depending on their CSR performance, before the contractual expiry date. Suppliers are usually paid within 60 days of the end of the month from the date when the goods leave the factory, but they can request payment in advance. Through this programme, suppliers can finance their short-term investments, such as the purchase of equipment or raw materials. Suppliers outside of France and Europe who do not benefit from the programme are paid within 65 days of the end of the month. Under the LME, the law on economic modernisation in France and Europe, suppliers are paid within 45 days of the invoice date.
At our company, social responsibility is a very important issue that affects everyone. That’s why Pimkie CEO, Philippe Favre, is also responsible for managing the environmental and social impact of our business:
“Today, it has become essential, especially in the fashion and textiles sector, which is being challenged to take action over its environmental and social impact, to meet the expectations of all our stakeholders concerning CSR (Corporate Social Responsibility).
We’re not perfect, but we’re committed to progress, we make commitments and we stick to them. All of Pimkie's teams, starting with its board of directors, are committed to working towards this goal.
Our achievements include the following:
- Pimkie uses almost no materials of animal origin, for reasons of animal welfare and the environmental impact of livestock breeding.
- We’re using more and more recycled fibres to make our products, which helps minimise depletion of the planet's resources.
- We are extremely vigilant about the manufacturing conditions for our products, particularly from a human and environmental point of view.
These are just a few examples of our approach, and you’ll discover more about our efforts every day in our stores, on our websites and from our partners. Thank you for your loyalty to our brand and for the progress you have helped us make.”
To summarise, the corporate social responsibility manager reports to general management. This probably doesn’t mean much to you, but it’s really important, because it shows how much we care about all these issues at Pimkie. We recently created project manager and CSR stylist positions to implement this strategy among all our teams. To let you know, the CSR project manager’s job is to set up, coordinate and monitor the progress of existing or new projects, which they or their colleagues may have launched. As for a CSR stylist, their role is to integrate the CSR issues we just talked about, into product design. A specific steering committee, made up of people from the various Pimkie departments, has been set up to lead CSR-related projects. This committee should make us more efficient by synchronising all our efforts and solving any potential problems. We’re also working on a materiality analysis (a tool for developing a CSR strategy that is used to assess company challenges), as well as setting CSR-related objectives for all our employees and activities.
According to the “Act for the freedom to choose one's future career” passed on 5 September 2018, every company must evaluate its performance on professional equality. The Professional Gender Equality Index is evaluated using several indicators.
- On the gender pay gap, Pimkie scored 38 out of 40 points in 2019
- That same year, for access to pay raises between women and men, we scored 20 out of 20
- For gender equality in access to promotions in 2019, we scored 15 out of 15
- We got the same score for the proportion of employees who received a pay rise after returning to work from maternity leave in the same year.
- We were also rated 10 out of 10 in 2019 for the number of female employees among the highest paid.
> Based on these results, our company scored 98 out of 100 points overall in 2019, compared to a score of 83 out of 100 in 2018.
In 2021, our rate evolved to 97 out of 100.
Not bad, right?! This score is reviewed during the first quarter of each year, so we can’t wait to see what happens next time! We'll keep you posted, as usual.
In September 2020, an internal agreement relating to professional equality between women and men and quality of life at work was concluded with our social partners: it notably includes measures on professional mobility, support for employees even in the event of prolonged absence or not, and the adaptation of working time in the event of pregnancy.
The French law called SAPIN 2 imposes that companies set up several tools to fight against corruption. This law requires that we check on our suppliers to make sure they don’t participate in corruption. We have a zero-tolerance policy about corruption and bribery. The disrespect of our internal rules can lead to heavy penalties, including dismissal, or criminal penalties.
Various internal and external risk measurement and control methods have been established, and our code of ethics also defines the behaviors to be avoided and those that are likely to be characterized as acts of corruption. Training has also been adapted for all employees. An internal alert system is in place: it is intended to allow internal and external employees to report any unethical behavior (corruption but also harassment, discrimination, etc.).
As a French company, our rights and obligations depend on the French Labor Code: it determines all relations between the employer and its employees throughout the duration of the employment relationship (hiring, contracts, working conditions, duration and working time, suspension or termination of the employment contract, wages and benefits, health and safety, freedom of association, right to organize, collective bargaining, harassment and violence, etc…). We are also dependent on internal collective agreements, which in some cases have more favorable provisions for employees (in the area of health or maternity and parental leave, for example).
Sensitive to human rights, we pay great attention to the subjects of discrimination, diversity and inclusion, which we take into account in the processes of recruitment and integration of employees. We do not tolerate any form of discrimination, physical or moral harassment for any reason. Similarly, any discrimination based in particular on origin, sex, disability, family situation, pregnancy, state of health, sexual orientation, age, political and philosophical opinions, trade union activities, membership or non-membership, real or supposed, of an ethnic group, nation or religion is prohibited. As also specified in the French Labor Code, a social and economic committee (CSE) is mandatory in companies with at least 11 employees, which is the case for Pimkie. The members of the CSE are elected by the employees for a maximum term of 4 years, and contribute to promoting health, safety and working conditions.
Pimkie employees have the option of using a counseling service to help each of them in times of difficulty or crisis, whether on an emotional or practical level.
An internal code of ethics was created in 2021 and distributed to all employees. In particular, it includes a section on the procedure to follow in the event of a problem in labor relations (harassment, threats, etc.).
All of the legal obligations to which we respond can be consulted on the official website of the French government https://travail-emploi.gouv.fr (in particular the duration of maternity leave: minimum 16 weeks; or paternity leave: 11 days, and any other type of information covered by French law in the context of work).
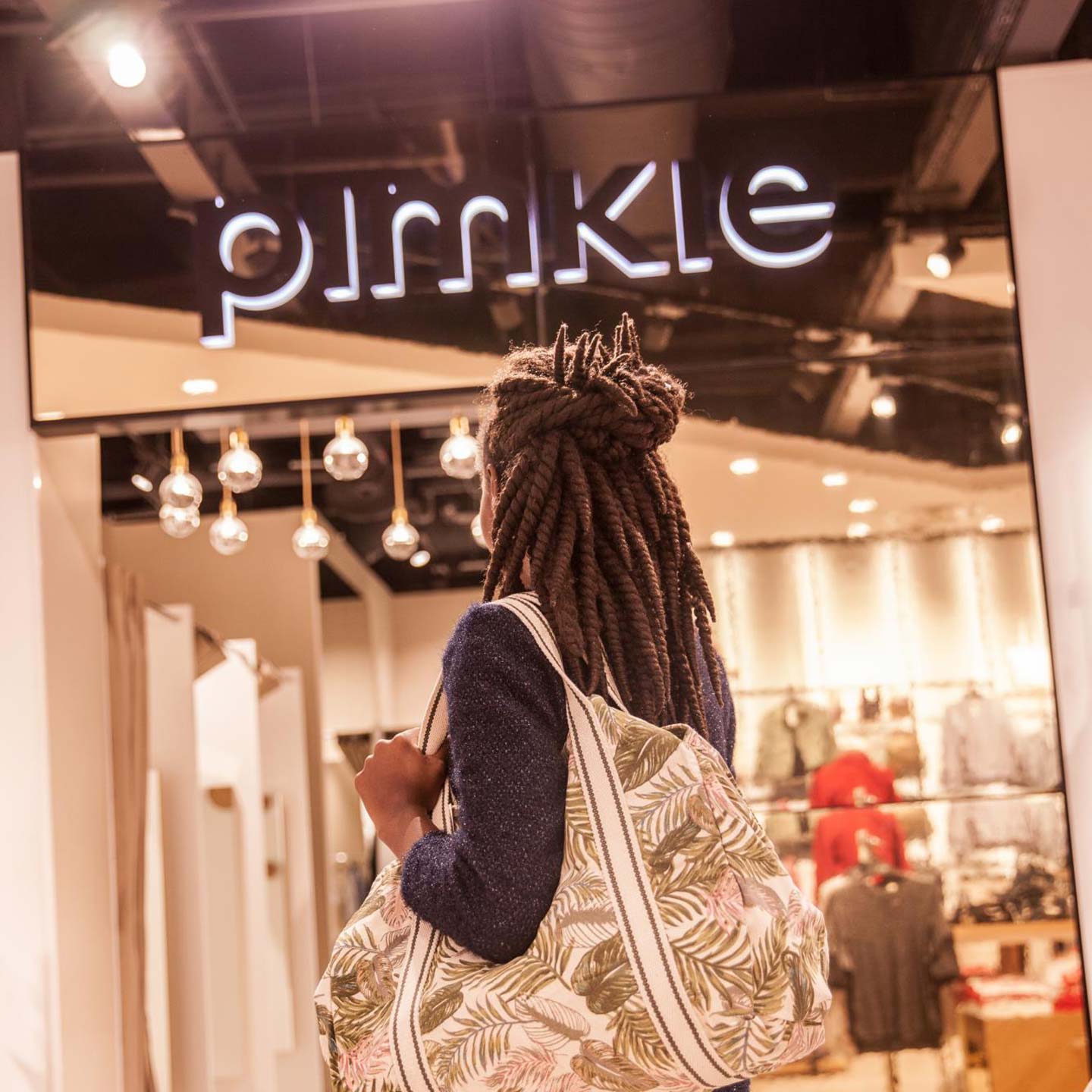
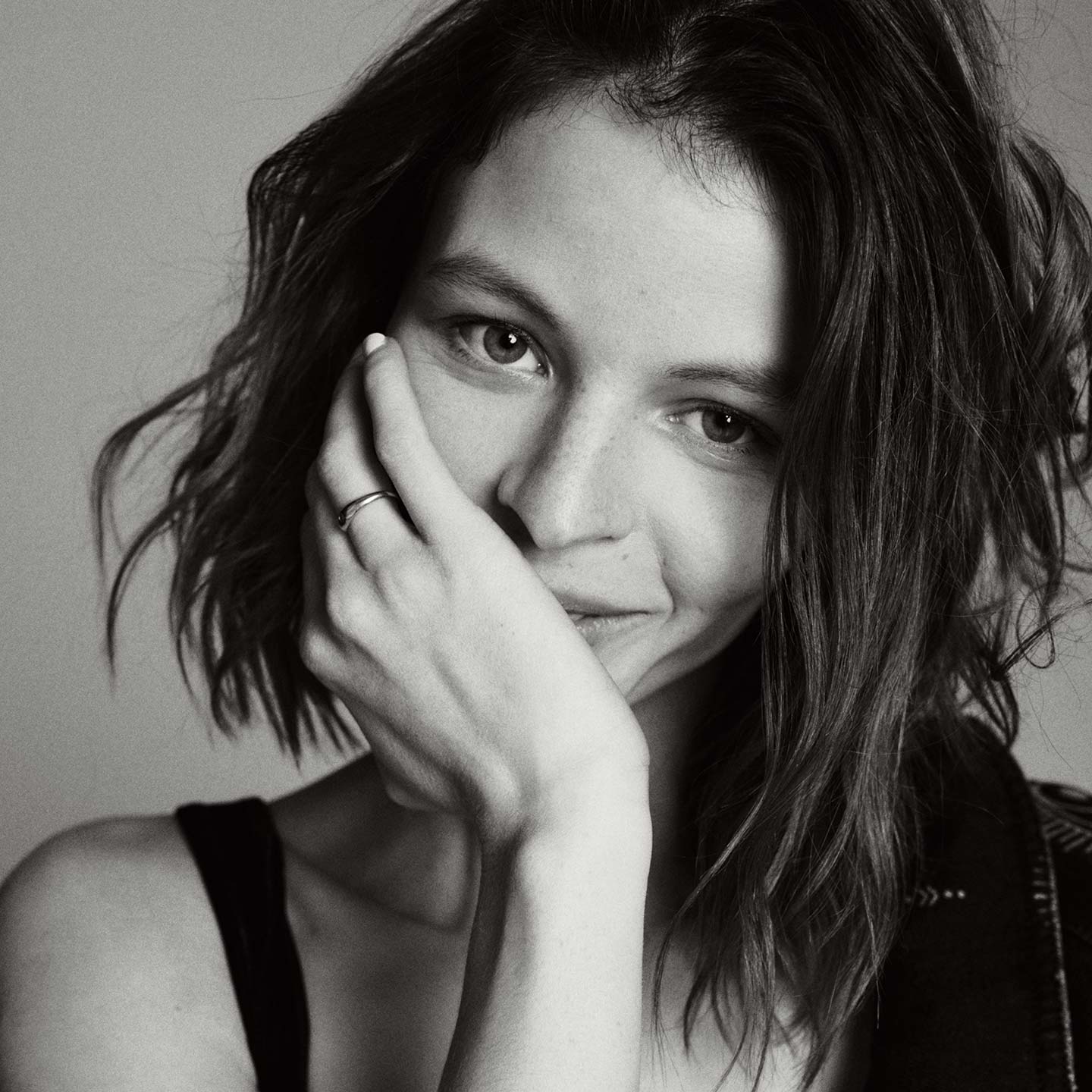
Using animal fibres in our clothes has an impact on animal welfare and the environment, because grazing or soy feed can often result in deforestation. So, we’ve also decided to prioritise the use of recycled wool. And what’s more, if you take a look at our website, you’ll see that there’s no leather, no angora, no real fur, and not even mother of pearl.
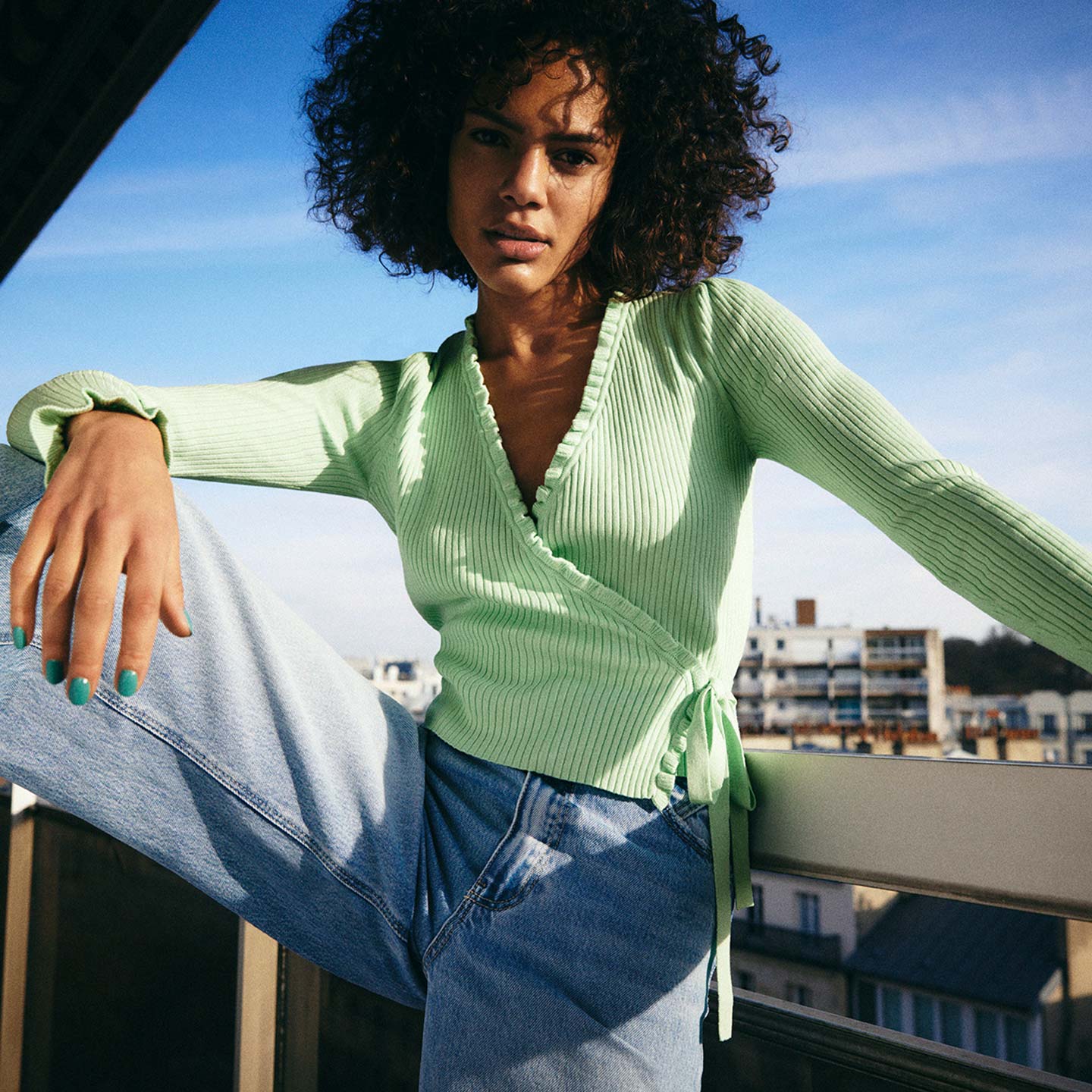
You’ll have realised by now, we like challenging ourselves. So, we took 10 of our best-selling products in 2018 and carried out a life cycle analysis on them. We analysed the environmental impact of these products, from raw material production to end of life. This analysis has shown that raw material production is the most harmful to the environment, followed by dyeing. The main impacts are air pollution (25% of overall impact), greenhouse gases (24%), the use of non-renewable resources (oil, for example) (14%), water consumption (10%), acidification (7%), etc.). Here’s a small graph so you can see for yourself:
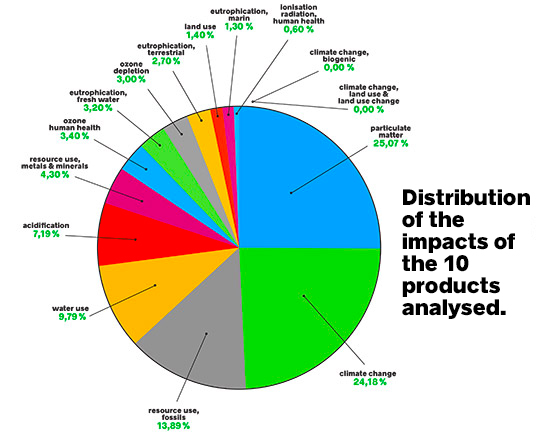
In short, this confirmed what we thought: we should definitely use more and more recycled materials in our products and keep these life cycle analyses up-to-date so we know where we stand and can improve faster. Without that, there'll be no real lasting change.
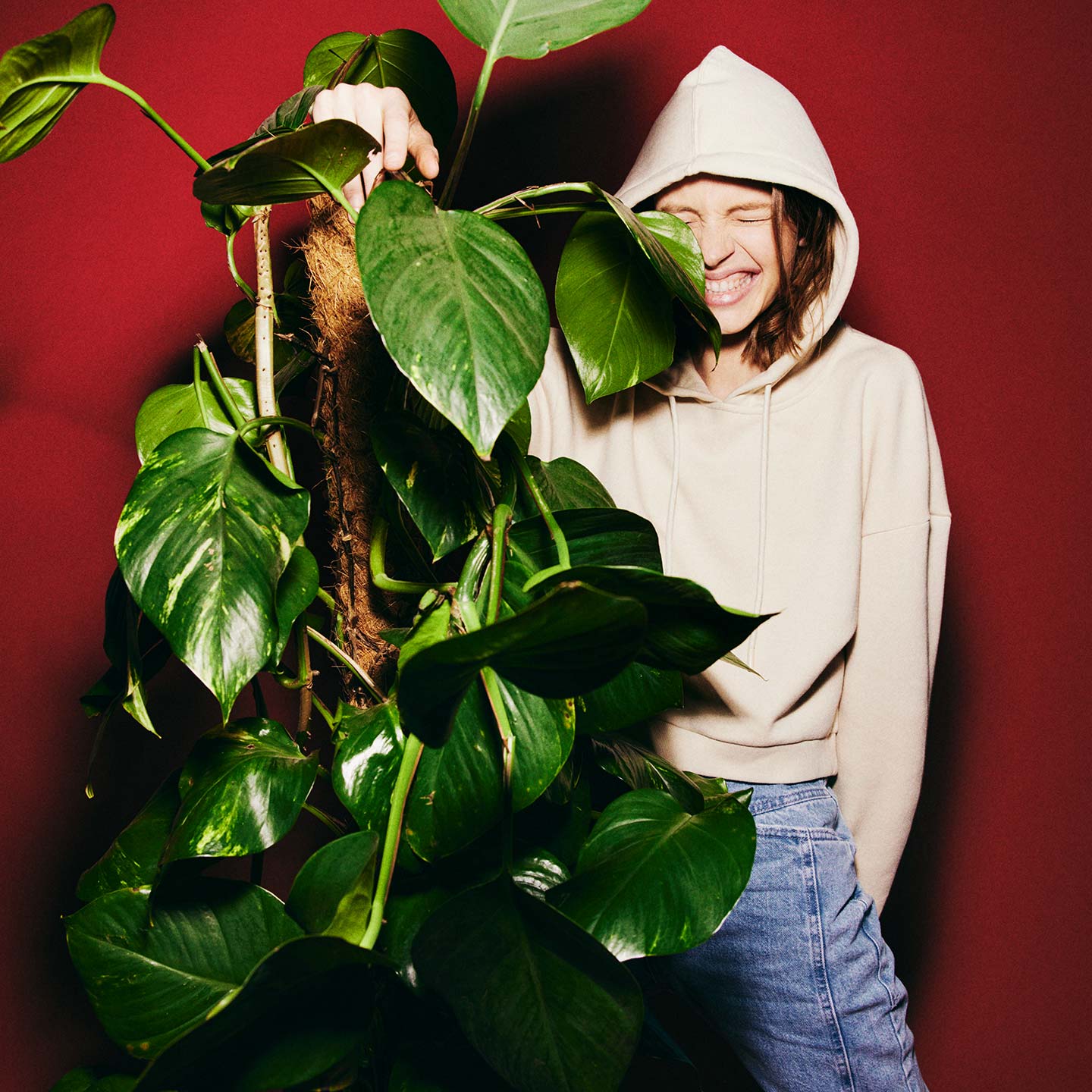
We decided to stop leaving the doors of our stores open during hot weather and in winter to reduce our electricity consumption. You can make sure of it the next time you come to see us!
We have also entered into a contract with our energy suppliers that ensures the use of renewable energy to supply our stores and our head office, as well as the reintegration of renewable energy into their energy network. Today, it is impossible to trace the share of renewable energies that we use (concretely, we cannot put a small tracer on energy). On the other hand, according to our supplier, our energy sources are mainly French and what is called the "electrical mix" (the distribution of the different sources of electricity) in France is estimated as follows:
- - nuclear (about 67%)
- - hydraulics (about 13%)
- - thermal energy (about 7.5%)
- - solar energy (about 2.5%)
- - bioenergy (about 1.9%)
Our warehouses recycle the boxes containing the products when they arrive. In store, you may have noticed that since June 2019, you too can reduce your environmental impact and get your receipt by email. In France, this new practice saved 200 km of paper in 5 months, or 1,500 kg of paper, or 765,000 litres of water!
analysis
We’ve also made sure that we can quantify our emissions in France. Click here for all the info in detail: See full analysis
We’re not pretending that we’re the only ones talking about the environment: some of the biggest names in fashion are increasingly committed to the climate, biodiversity and the oceans, and we’re proud to be part of it! We’re 100% aware of the fashion sector’s current environmental impact, and we know that urgent action is needed. The Fashion Pact sets ambitious but achievable targets to limit our impact in 3 priority areas: climate (by mitigating climate change), biodiversity (by reversing biodiversity loss within 10 years), and the oceans (by combating the critical loss of ocean function caused by climate change and pollution). The Pimkie team supports the UN’s Sustainable Development Goals, which are part of the Fashion Pact.
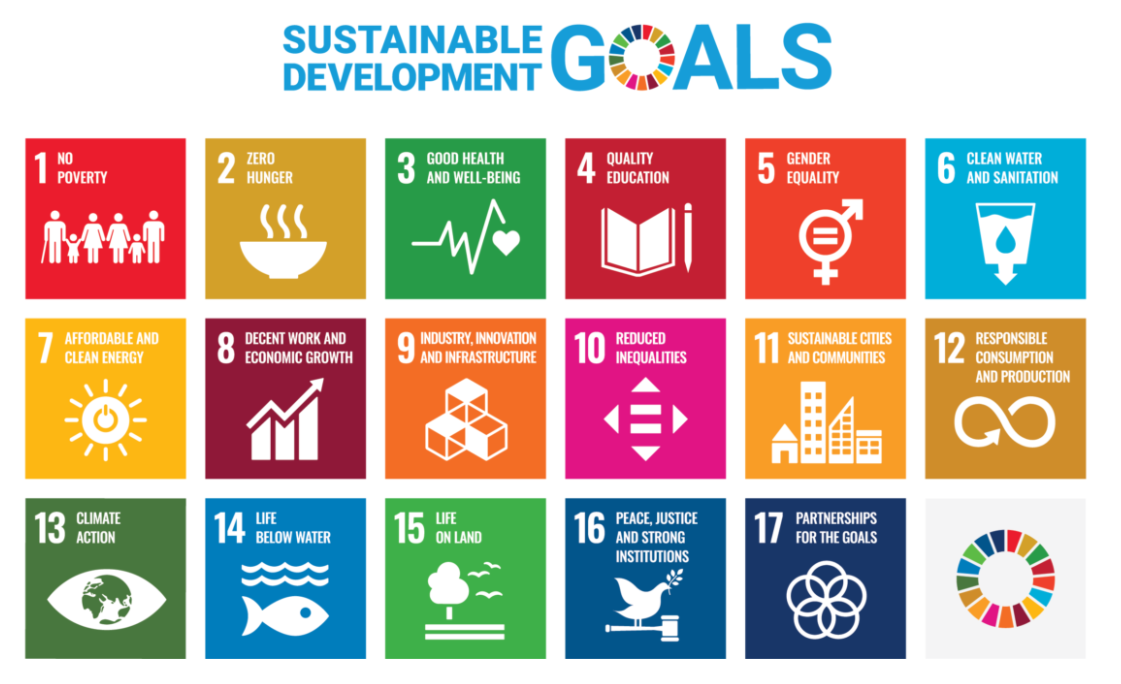
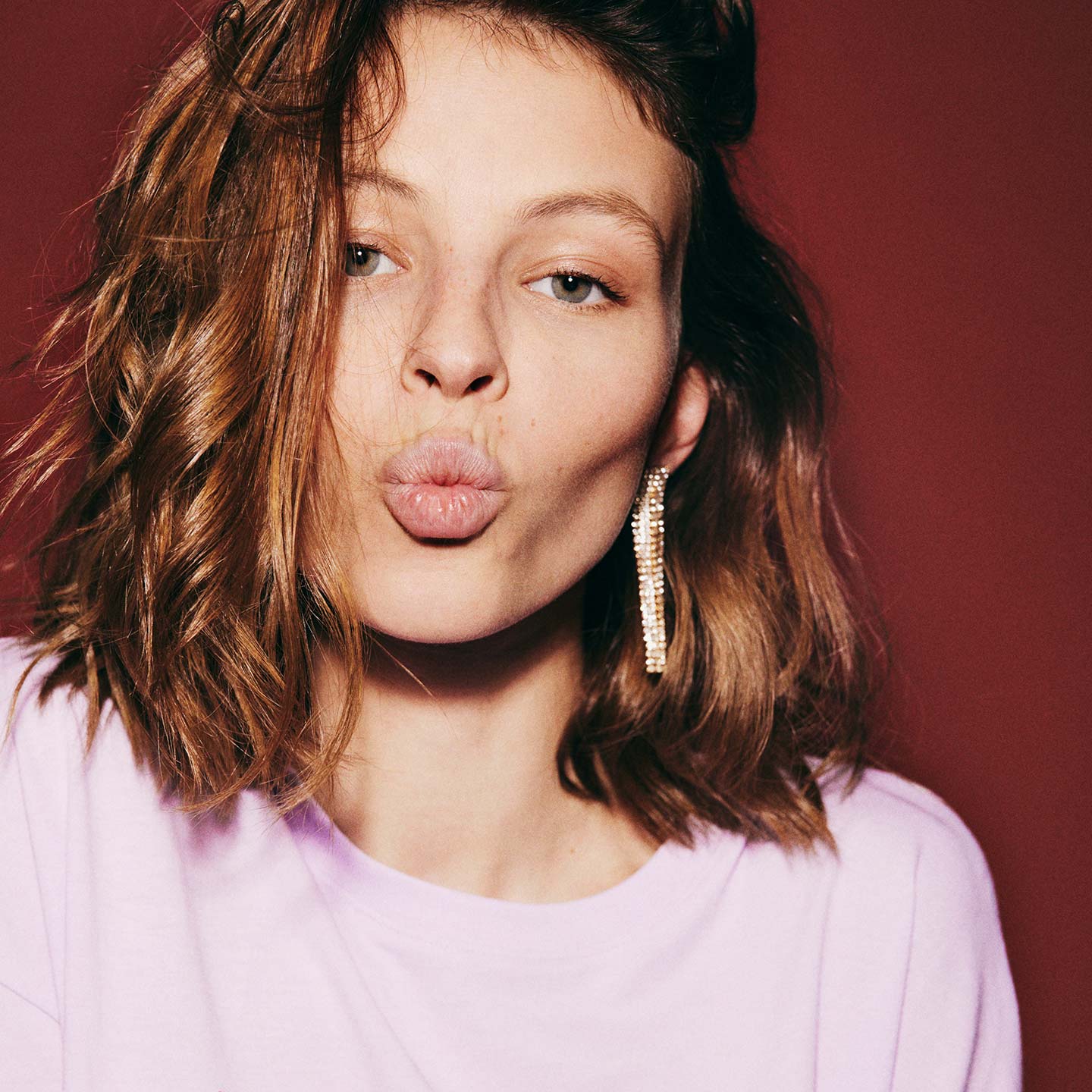
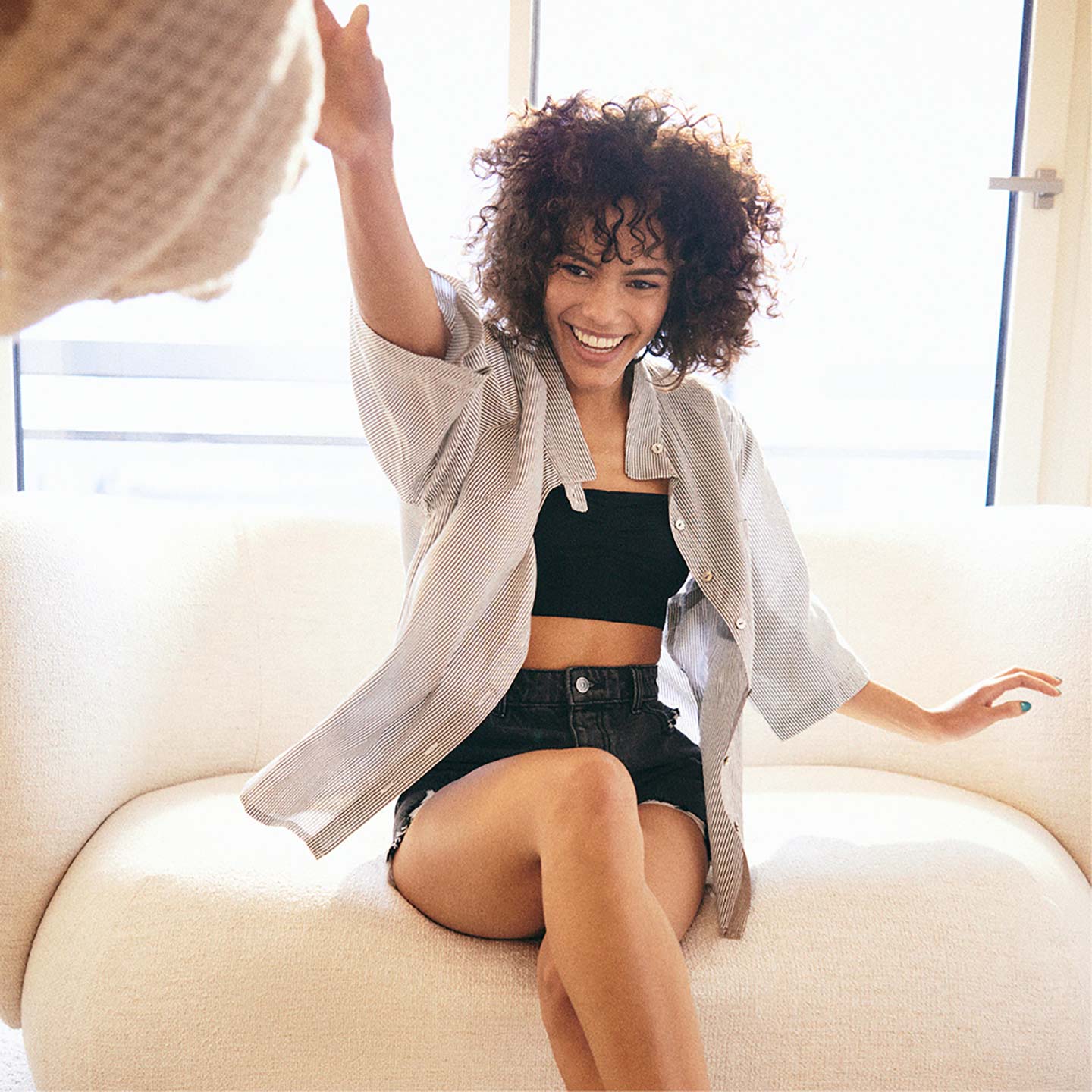
EP&L is a kind of technique for calculating environmental performance. It’s used to measure and put a monetary value on the environmental impact of a brand across its entire chain of influence and according to several criteria, such as greenhouse gas emissions, impact on water, waste production, etc. Our EP&L analysis has shown that our impact is estimated at €74 million and that 72% of this impact is due to the raw materials used, as well as the dyeing processes. Click here to see the full analysis: EP&L
Team Pimkie is also a member of Textile Exchange, a non-profit organisation that helps brands adopt more environmentally friendly practices, such as using recycled materials or reducing greenhouse gases. The Textile Exchange gives us lots of helpful tools for market research and scientific data, etc. Want more info? Click here.
Initiated by the Fashion Revolution collective, which encourages everyone to question the environmental and social impacts of the manufacture of clothing, the Fashion Transparency Index is a benchmark that evaluates each year the amount of data made publicly available by brands, based on nearly 240 indicators. The index takes into account relations with suppliers, commercial practices and their effects on workers, on the various communities concerned and on the environment. The Fashion Transparency Index identifies possible areas of progress for brands, and encourages them to improve and communicate this in the fairest way possible.
In 2021, Pimkie scored 29%, which places the brand 78th out of the top 250 fashion brands and retailers! You can find the full index and assessment conditions here.